Creating a MapleSim digital model gives a virtual representation of your product and is the first step to applying digital twins across your operations.
Simulations and digital twins both utilize digital models to replicate a system’s various processes, but a digital twin presents a virtual environment that stays up-to-date, making it more flexible for applications across a product lifecycle. A digital twin can be used during R&D and production all the way through to monitoring and maintenance. It unlocks synergies by providing a single source of truth across every department, from design to training to marketing.
The primary uses of Digital Twins are:
- Descriptive – Design and validate the product before it exists in the real world
- Informative – Gathering operational data at scale to compare tests with the model
- Predictive - Predict and show what will happen across various real-world scenarios
- Living Digital Twin - Analyze how your product behaves and is used in the real world over time
MapleSim makes it simple to get started by building a digital model of your product, which can be exported into automation development software. As operations grow, MapleSim models can scale up by connecting bi-directionally with a cloud-based digital twin platform, such as AWS IOT Twinmaker or Oracle Cloud Anomaly Detection service.
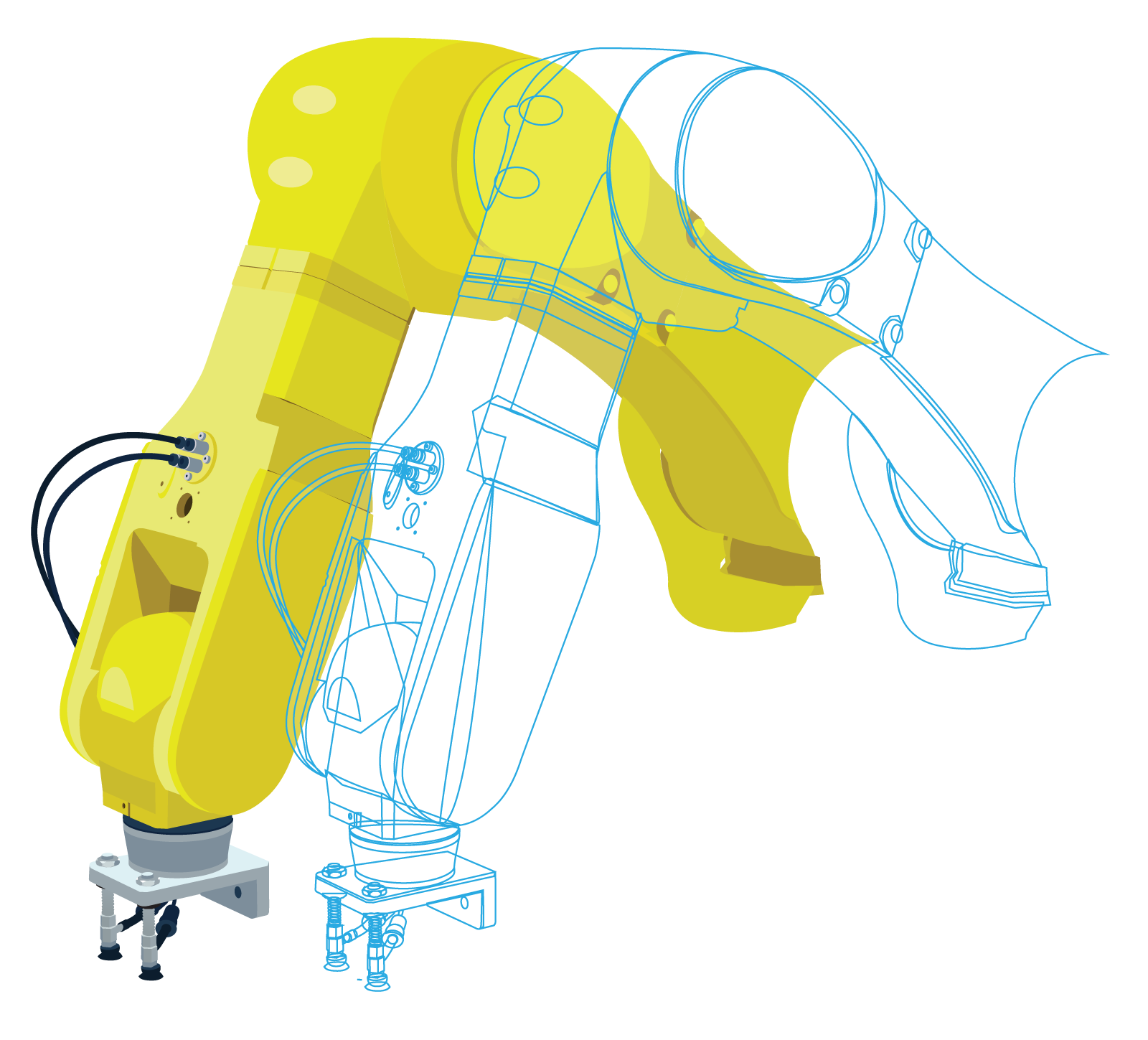
Model-based digital twins, such as those developed using MapleSim, have greater accuracy and can represent a broader range of scenarios than simulations developed exclusively from historical operational data, leading to use in a greater variety of engineering tasks:
- Conceptual Development: Very early experimentation with design concepts in a model that predicts the dynamic behavior provides powerful insight and allows engineers to make more informed decisions.
- Virtual Commissioning: Long before the first build, engineers can predict the steady-state and transient loads that the actuators will face during their duty cycles. This helps to properly size the actuators to eliminate failure, while avoiding over-engineering.
- Online Diagnostics: Simulating the Digital Twin in parallel with the real machine can provide valuable insight into where a problem might arise as the machine’s response drifts from the model as it ages.
- Virtual Sensors: Since the dynamic response of the Digital Twin is built on rigorous physical laws, certain calculated properties may be sufficient to use as inputs to the control system, either to replace a faulty sensor until it can be fixed, or eliminate its use altogether. Both scenarios can provide a significant reduction in costs.
- Predictive Maintenance: There are many factors that determine the maintenance schedule for a machine, but one factor is frequently overlooked because it is difficult to predict without a Digital Twin. This factor is the impact of dynamic loading on bearings, gears, and motors, caused by changes in the duty cycle. Putting a Digital Twin through a proposed duty cycle can help to determine the loads on these components, which can be used to calculate the impact on the component’s life.
- Product Enrichment: A Digital Twin allows manufacturers to ask important questions like, how fast can a machine safely perform an operation (cycles per minute) or how heavy of a load can it move, without needing to push requests back through to engineering. This allows manufacturers to provide greater innovations and differentiate themselves from their competition.
- Sales Tool: Outside of the engineering department, the Digital Twin can be used to qualify customer specifications. For customers, this information can help validate the performance of a machine given different payloads or operating conditions, without needing a full consultation by an engineer.